In a hardware store, the paint department is often a cornerstone of customer satisfaction and profitability. However, if your store relies on outdated paint dispensers, you may be unknowingly undermining your business. While older dispensers may seem functional, their hidden inefficiencies can lead to wasted resources, dissatisfied customers, and operational headaches. Let’s explore the real cost of keeping outdated equipment and why upgrading is essential for your success.
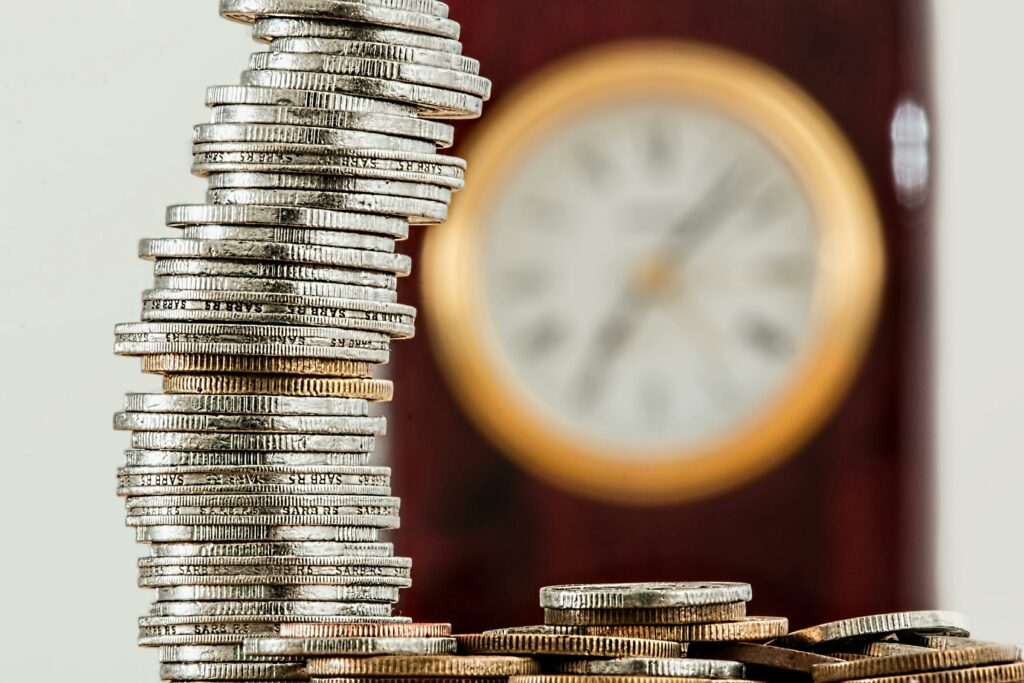
Negative Impacts on Your Business
Inconsistent Color Matching
Older dispensers lack the precision and technology of modern equipment, resulting in inaccurate color matching. Miss-tints not only waste materials but also erode customer trust, leading to fewer repeat customers.Increased Downtime and Maintenance Costs
Aging dispensers are prone to breakdowns, requiring frequent repairs that disrupt workflow. The downtime and repair expenses quickly add up, cutting into your profitability and productivity.Slower Operations
Old dispensers can’t keep up with the speed demands of modern customers. Delays in dispensing paint during busy periods frustrate customers and can result in lost sales.Higher Material Waste
Without advanced technology to regulate flow and dispensing, outdated machines waste colorants and base paint. This not only impacts your bottom line but also raises environmental concerns.Damaged Reputation
Consistently poor performance in your paint department reflects poorly on your store. Dissatisfied customers may leave negative reviews or switch to competitors who provide better services with modern equipment.
The True Cost of Old Equipment
- Wasted Resources: Studies show that inaccurate color matching and inefficient dispensers can result in up to 20 of customers will not return to a store if they experience poor service or incorrect orders, including miss-tints.
- Operational Downtime: Frequent dispenser repairs can lead to 10-15% loss in daily productivity, particularly during peak business hours.
Conclusion
An old paint dispenser may seem cost-effective at first glance, but its hidden inefficiencies can significantly impact your hardware store’s profitability and reputation. From wasted resources to dissatisfied customers, the cost of holding onto outdated equipment outweighs the investment in upgrading. Modern dispensers like the X-PROTINT or AT1600 by Fluid Management deliver speed, precision, and reliability, ensuring your paint department meets today’s demands.
Don’t let outdated equipment hold your business back—upgrade to a modern dispenser and see the difference in your operations and customer satisfaction. Contact Harper Inc. today to learn more about the latest dispensing technology!